У нас можно недорого заказать курсовую, контрольную, реферат или диплом

«Рассчет и проектирование стадии денитрации отработанных кислот производительностью 80тсут, 98%-ой азотной кислоты» - Дипломная работа
- 86 страниц(ы)
Содержание
Введение
Заключение
Список литературы
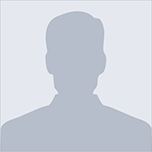
Автор: Pingvin78
Содержание
ВВЕДЕНИЕ
1. Аналитическая часть
1.1 Историческая справка
1.2 Общие сведения о концентрировании серной кислоты
1.2.1 Физико-химические свойства серной кислоты
1.2.2 Раскисление серной кислоты при ее концентрировании
1.3 Методы концентрирования серной кислоты
1.4 Выбор и обоснование метода производства
1.5 Химизм основных и побочных реакций
2. Расчетно-технологическая часть
2.1 Описание и режимы технологического процесса
2.1.1 Краткое описание технологического процесса
2.1.2Денитрация и концентрирование азотной кислоты
2.1.3 Контроль технологического процесса концентрирования азотной кислоты
2.1.4 Улов нитрозных газов
2.1.5 Контроль технологического процесса улова нитрозных газов
2.1.6 Концентрирование серной кислоты
2.1.7 Технологический процесс и режим работ колонны концентрирования серной кислоты БМКСХ
2.1.8 Порядок пуска вихревой колонны
2.1.9 Останов вихревой колонны
2.2.2 Упаковка, маркировка регенерированной серной кислоты
2.2.3 Прием кислот со стороны
2.3 Техническая характеристика сырья, полуфабрикатов и продуктов
2.4 Материальный баланс производства
2.5. Расчет теплового баланса вихревой колонны
2.6 Выбор и расчет технологического оборудования
2.7 Механический расчет вихревой ферросилидовой колонны концентрирования серной кислоты
3 ТЕХНИКА БЕЗОПАСНОСТИ И ПРОТИВОПОЖАРНАЯ ПРОФИЛАКТИКА
4 АВТОМАТИЗАЦИЯ
5 ТЕХНИКО-ЭКОНОМИЧЕСКОЕ ОБОСНОВАНИЕ ПРОЕКТА
Заключение
Список использованных источников
Введение
Азотная и серная кислоты находят широкое применение в химической промышленности; ни одно нитросоединение не может быть получено без азотной и, как правило, без серной кислот. Так, например, нитроцеллюлоза, используемая для получения целлулоида, кинопленки, линолеума и другой подобной продукции, нитроглицерин, являющийся составной частью динамитов и победитов, а также ряд взрывчатых веществ требуют применения азотной кислоты для образования нитрогрупп и серной кислоты для связывания реакционной воды.
При образовании нитросоестинении получается большое количество отработанных кислот, которые необходимо разделить на составные части и укрепить до нужной концентрации. Правильно построенный кислотооборот должен быть таким, при котором все отработанные кислоты после регенерации и концентрирования полностью использовались бы на заводе. При идеально построенном кислотном хозяйстве и совершенных схемах технологического процесса азотная кислота должна расходоваться только на реакцию образования нитросоединений, а серная кислота, которая в реакции не участвует, вообще не должна теряться. Практически это выглядит так: азотная кислота, кроме реакции образования основного продукта, частично теряется с промывными водами при стабилизации и участвует в побочных реакциях, получения малостойких эфиров, разрушающихся при промывке; кроме того, азотная кислота улетает в вентиляционную систему и далее в поглотительную систему, а вследствие недостаточно совершенной схемы,
азотная кислота не вся улавливается и примерно 5% теряется в атмосферу; наконец, имеют место потери при концентрировании азотной кислоты. Серная кислота расходуется на образование сульфоэфиров, разрушающихся при промывках, и теряется при стабилизации продукта; кроме того, имеются потери при регенерации отработанной смеси и концентрировании серной кислоты.
Для покрытия указанных выше потерь на заводах в зависимости от потребности строятся собственные цехи азотной и серной кислот или же свежие кислоты завозятся со стороны, но ни в коем случае, не следует допускать вывоза слабых кислот с завода /3/.
В настоящее время развитие производств, применяющих смесь азотной и серных кислот в качестве нитрующего агента, привело к получению огромных количеств отработанных кислотных смесей. Эти смеси с экономической точки зрения необходимо регенерировать и в необходимых расчетных концентрациях возвращать обратно в производственный цикл, тем самым удешевляя единицу себестоимости готовой продукции.
Состав тройных смесей HNO3 – H2SO4 – H2O, поступающих на регенерацию, колеблется в довольно широких пределах. В одних случаях они представляют сильно разбавленные кислотные смеси с содержанием азотной кислоты 5-10%, в других случаях отработанные кислоты содержат 1-2% азотной кислоты и 65-70% серной кислоты, в которой растворены окислы азота N2O3, образующие нитрозилсерную кислоту HNSO5.
Регенерация таких смесей представляет собой определенные трудности и требует изыскания все новых и новых способов, обеспечивающие нормальное ведение процесса разгонки отработанных кислот, а также получение азотной и серной кислот, которые по своим качествам и техническим характеристикам не уступают свежим кислотам применяемым для нитрации /1/.
Заключение
Целью данного проекта является рассчитать и спроектировать стадию денитрации отработанных кислот производительностью 80т/сут, 98%-ой азотной кислоты.
В соответствии с целью, задачами и исходными данными выполнен курсовой проект, по результатам которого можно сделать следующие выводы:
1. Был рассмотрен технологический процесс денитрации рекуперированных и уловленных кислот с последующим концентрированием азотной кислоты и регенерацией серной кислоты с подробным изучением технологического процесса и режима работ колонны концентрирования БМКСХ.
2. Проведен сравнительный анализ существующих аппаратов для денитрации азотной кислоты, и выявлены основные достоинства и недостатки.
3. Осуществлены необходимые материальные и технологические расчеты.
4. Описаны требования и меры безопасности при эксплуатации производства.
5. Предложена более эффективная конструкция вихревой колонны. Усовершенствования направлены на снижение гидравлического сопротивления, металлоемкости и высоты аппарата и вторичного брызгоуноса кислоты, повышение эксплуатационной надежности вихревой технологии.
Список литературы
1. Атрощенко, В.И. Технология азотной кислоты / В.И. Атрощенко, С.И. Каргин. - М.: Химия, 1970. - 493с.
2. Амелин, А.Г. Производство серной кислоты / А.Г. Амелин, Е.В. Яшке. - М.: Высшая школа, 1974. - 223с.
3. Лебедев, А.Я. Установки для денитрации и концентрирования серной кислоты / А.Я. Лебедев.- М.: Химия, 1972. - 240с.
4. Амелин, А.Г. Технология серной кислоты / А.Г. Амелин. - М.: Химия, 1983. - 340с.
5. Производство азотной кислоты: технологический регламент/ ФКП «КП КПЗ», - Казань, 1974. – 300с.
6. Касаткин, А.Г. Основные процессы и аппараты химической технологии / А.Г. Касаткин. - М: Химия, 1971. - 783с.
7. Павлов, К.Ф. Примеры и задачи по курсу процессов и аппаратов химической технологии / К.Ф. Павлов, А.Т. Романков, А.А. Носков. - А.: Химия,1987. - 705с.
8. Автоматические приборы, регуляторы и вычислительные системы: Справочное пособие / Б.Д. Кошарский, Т.У. Бедновская, В.А. Бек и др. - Л.: Машиностроение, 1976. - 448с
9. Лащинский, А.А. Основы конструирования и расчета химической аппаратуры / А.А Лащинский, А.Р. Толчинский.: Л.: Машиностроение, 1970. - 752с
10. Основные процессы и аппараты химической технологии: Пособие по проектированию / Под. ред. Ю.И. Дытнерского.- М: Химия, 1989. - 546с.
11. Фарзанс, Н.Г. Технологические измерения и прибоы / Н.Г. Фарзанс, П.В. Ильясов. - М.: Высшая школа,1982.-260с.
12. Макаров, Г.В. Охрана труда в химической промышленности / Г.В. Макаров.- М:Химия, 1989.-495с.
13. ГОСТ 7.1-2003. Издание. Примеры библиографического оформления документов. – М.: Изд-во стандартов, 2004.-7с
14. ГОСТ 14192-96. Издание. Транспортная маркировка. – М.: Изд-во стандартов, 1997.- 12с
15. ГОСТ 19433-88. Издание. Нанесение знаков безопасности на упаковку. – М.: Изд-во стандартов, 1989.-3с
16. ГОСТ 10585-75. Издание. Технические условия на мазут. – М.: Изд-во стандартов, 1975.- 5с
17. ГОСТ 2184-77. Издание. Кислота серная регенерированная. – М.: Изд-во стандартов, 1977.- 7с
18. ГОСТ 701-78. Издание. Кислота азотная концентрированная. – М.: Изд-во стандартов, 1979.- 11с
19. ГОСТ 1500-78. Издание. Меланж кислотный. – М.: Изд-во стандартов, 1979.- 8с
20. ГОСТ5542-70. Издание. Газ природный. – М.: Изд-во стандартов, 1971.- 12с
Тема: | «Рассчет и проектирование стадии денитрации отработанных кислот производительностью 80тсут, 98%-ой азотной кислоты» | |
Раздел: | Промышленность и Производство | |
Тип: | Дипломная работа | |
Страниц: | 86 | |
Цена: | 500 руб. |
Закажите авторскую работу по вашему заданию.
- Цены ниже рыночных
- Удобный личный кабинет
- Необходимый уровень антиплагиата
- Прямое общение с исполнителем вашей работы
- Бесплатные доработки и консультации
- Минимальные сроки выполнения
Мы уже помогли 24535 студентам
Средний балл наших работ
- 4.89 из 5
написания вашей работы
Не нашли, что искали?
Воспользуйтесь поиском по базе из более чем 40000 работ
Предыдущая работа
Гранулирование плава аммиачной селитры. Экспериментальная установкаСледующая работа
Производство кефира
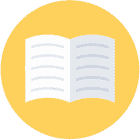
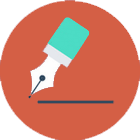
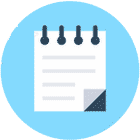

-
Курсовая работа:
Получение формальдегида окислительным дегидрированием метилового спирта.
19 страниц(ы)
Задание 3
1. Опишите свойства формальдегида, области его применения 5
2. Проведите сравнение методов получения формальдегида из различных видов сырья. 73. Опишите физико-химические свойства системы, положенной в основу получения формальдегида из метанола. На основе анализа этих свойств проведите обоснование оптимального варианта технологического режима, типа технологической схемы 10РазвернутьСвернуть
4. Приведите чертеж и описание технологической схемы получения формальдегида окислительным дегидрированием метанола. 14
5. Рассчитайте и составьте материальный баланс процесса получения 16
Список использованных источников 20
-
Дипломная работа:
Рассчитать и спроектировать стадию абсорбции окислов азота в производстве азотной кислоты
128 страниц(ы)
ВВЕДЕНИЕ 3
1 ЛИТЕРАТУРНЫЙ ОБЗОР 4
1.1 Историческая справка 4
1.2 Описание технологии 7
1.3 Физико-химические основы получения азотной кислоты 191.4 Способы окисления оксида азота 25РазвернутьСвернуть
1.5 Недостатки существующей технологии и пути ее совершенствования 33
1.7 Аэродинамика вихревого контактного устройства 43
2 ЭКСПЕРИМЕНТАЛЬНАЯ ЧАСТЬ 54
2.1 Описание методики 54
2.2 Обработка результатов эксперимента 59
3 РАСЧЕТНАЯ ЧАСТЬ 63
3.1 Материальный баланс 63
3.2 Тепловой баланс 80
3.2 Расчет толщины стенки 82
3.3 Расчет днища 82
3.4 Расчет крышки 83
3.5 Расчет фланцевого соединения 84
3.6 Расчет вихревого контактного устройства 87
5 МЕТРОЛОГИЧЕСКАЯ ПРОРАБОТКА 89
5.1 Описание функциональной схемы автоматизации установки 89
5.2 Обработка результатов прямых измерений 89
6 ОБЕСПЕЧЕНИЕ ПРОИЗВОДСТВЕННОЙ И ЭКОЛОГИЧЕСКОЙ БЕЗОПАСНОСТИ 99
6.1 Характеристика производственной и экологической опасности объекта 99
6.2 Расчет освещения 99
6.3 Метеоусловия 101
6.4 Вентиляция и отопление 102
6.5 Шум и вибрация 102
6.6 Индивидуальные средства защиты 103
6.7 Электробезопасность 103
6.8 Пожарная безопасность 106
6.9 Молниезащита 107
6.10 Экологичность работы 108
7 ПАТЕНТНЫЕ ИССЛЕДОВАНИЯ 109
8 ЭКОНОМИЧЕСКОЕ ОБОСНОВАНИЕ 118
8.1 Составление сетевого графика 118
8.2 Затраты на основные и вспомогательные материалы 119
8.3 Энергетические затраты 119
8.4 Фонд заработной платы 120
8.5 Накладные расходы 120
8.6 Амортизационные отчисления 121
СПИСОК ИСПОЛЬЗОВАННЫХ ИСТОЧНИКОВ 123
-
Дипломная работа:
Разработка станции технического обслуживая на 11 постов в городе Перми
140 страниц(ы)
ВВЕДЕНИЕ 5
1 АНАЛИЗ ХОЗЯЙСТВЕННОЙ ДЕЯТЕЛЬНОСТИ СТО 7
1.1 Организация технологических процессов ТО легковых автомобиле 161.2 Выбор метода организации производства СТО 19РазвернутьСвернуть
1.3 Организация производственного процесса СТО 19
1.4 Организация работ ТО и ТР легковых автомобилей 21
2. ТЕХНОЛОГИЧЕСКИЙ РАСЧЕТ СТО 21
2.1 Исходные данные 21
2.2 Расчет годового объема работ СТО 31
2.2.2 Расчёт числа автомобилей, обслуживаемых СТО 36
2.2.3 Расчет годового объема уборочно-моечных работ 37
2.2.4 Расчет годового объема работ по приемке и выдаче автомобилей 37
2.2.5 Расчёт годового объема вспомогательных работ 38
2.3 Распределение годовых объемов работ по зонам и цехам 39
2.4 Расчет числа рабочих СТО 41
2.5 Расчет числа постов и автомобиле-мест ожидания 46
2.6 Расчет площадей помещений 49
2.7 Расчёт площади СТО 56
3 КОНСТРУКТОРСКАЯ ЧАСТЬ 58
3.1 Анализ конструкций стендов для диагностики подвески лекговых автомобилей.58
3.2 Описание стенда.64
3.2.1 Методы диагностирования амортизаторов и подвески.70
3.3 Расчет экцентрикового зажима.76
3.4 Подбор электродвигателя.78
3.6 Расчеты на прочность.81
3.7 Редуктор шевронный.83
3.8 Расчет на прочность валов.89
3.9 Выбор смазки редуктора.97
3.10 Проверка прочности шпоночного соединения.98
3.11 Проверка долговечности подшипника.100
3.12 Подбор муфты.101
3.13 Монтаж стенда.101
3.14 Техническое обслуживание стенда.102
4. БЕЗОПАСНОСТЬ ЖИЗНЕДЕЯТЕЛЬНОСТИ. 104
4.1 Безопасность жизнедеятельности.104
4.1.1 Анализ условий и охрана труда на предприятии.104
4.1.2 Требования безопасности при техническом обслуживании и ремонте автомобилей.108
4.1.3 Мероприятия по выполнению требований безопасности.115
4.2 Экологическая безопасность. 116
4.2.1 Негативное воздействие предприятия на окружающую среду и его снижение.117
4.2.2 Выбросы вредных и загрязняющих веществ в атмосферу.118
4.2.3 Обращение с отходами.120
4.2.4 Отчистка сточных вод от загрязнения.126
5. ТЕХНИКО-ЭКОНОМИЧЕСКОЕ ОБОСНОВАНИЕ ПРЕДПРИЯТИЯ 128
5.1 Этапы развития производства 128
5.2 Выбор метода экономической оценки инвестиций. 128
5.3 Расчет срока окупаемости 130
ЗАКЛЮЧЕНИЕ 139
СПИСОК ИСПОЛЬЗОВАННЫХ ИСТОЧНИКОВ 140
-
Дипломная работа:
100 страниц(ы)
ВВЕДЕНИЕ
1 Литературный обзор
1.1 Установки низкотемпературной сепарации
1.1.1 Основные факторы, влияющие на процесс НТС1.2. Сепарационное оборудованиеРазвернутьСвернуть
2 ТЕХНОЛОГИЧЕСКАЯ ЧАСТЬ
2.1 Выбор и обоснование технологической схемы производства
2.2 Характеристика сырья
2.3 Установка низкотемпературной сепарации с блоком входного сепаратора
2.4 Материальный баланс производства
2.5 Расчет основного оборудования
2.5.1 Выбор числа ступеней сепарации и давления в сепараторах
2.5.2 Расчет сепаратора
2.6 Расчет вспомогательного оборудования
3. МЕХАНИЧЕСКАЯ ЧАСТЬ
3.1 Исходные данные для конструктивного расчета аппарата
3.2 Расчеты на прочность основных узлов и деталей аппаратов
3.3 Эксплуатация оборудования
3.4 Ремонт и монтаж оборудования
3.4.1 Расчет такелажной оснастки
3.5 Специальная часть. Расчет системы регулирования
-
Курсовая работа:
Регенерация кислотных смесей и концентрирования слабой азотной кислоты
78 страниц(ы)
ВВЕДЕНИЕ
1. Аналитическая часть
2. Расчетно-технологическая часть
2.1. Описание технологической схемы
2.2. Стандартизация. Технологическая характеристика сырья2.3 Свойства готовых продуктов, сырья и полуфабрикатов.РазвернутьСвернуть
2.4. Химизм основных и побочных реакций
2.5. Расчет материального баланса отделения концентрирования HNO3
2.6. Расчет теплового баланса
3. Технико-технологическая часть
3.1. Выбор и расчет производительности основного и вспомогательного оборудования технологической схемы
3.2 Расчет количества аппаратов
4. Выбор и обоснование схемы автоматизации производственного процесса
5. Безопасность и экологичность проекта.
6. Строительно-монтажная схема здания цеха и компоновка оборудования
Заключение
Список использованных источников
-
Курсовая работа:
Производство таблеток глюконата кальция
52 страниц(ы)
Реферат
Перечень сокращений, условных обозначений, символов, единиц и терминов
Введение
1. Аналитическая часть1.1 Историческая справка о методах получения и использования продуктаРазвернутьСвернуть
1.2 Выбор и обоснование метода производства, химизм процесса
2. Расчетно-технологическая часть
2.1 Описание технологической схемы производства
2.2 Внесенные изменения по сравнению с аналогом и обоснование изменений, вносимых в проект
2.3 Техническая характеристика сырья, полуфабрикатов и продукта
2.4 Материальный баланс производства
2.5 Выбор и технологический расчет основного и вспомогательного оборудования
2.6 Механический расчет
2.7 Производственная и экологическая безопасность
Заключение
Список литературы
Приложения
-
Курсовая работа:
Расчет основных параметров горения и тушения пожаров
35 страниц(ы)
Введение
1. Горение газов
1.1. Общие закономерности кинетического режима горения
1.2. Влияние различных факторов на скорость распространения пламени1.3. Диффузионное горение газовРазвернутьСвернуть
1.4. Особенности горения газовых струй. Условия стабилизации пламени
1.5. Оценка дебита горящих газовых фонтанов
2. Методы тушения пожаров газовых фонтанов
3. Расчёт расхода воды, требуемого для прекращения горения газового фонтана
4. Задание на курсовую работу (вариант 1283):
5. Расчет основных параметров горения и тушения газового фонтана
Заключение
Список использованных источников
-
Отчет по практике:
Добыча и переработка нефти на предприятии ТНК-ВР
26 страниц(ы)
1. Историческая справка ООО «ТНК-ВР». 3
2. Производственная структура предприятия ООО «ТНК-ВР». 5
3. Характеристика основного процесса . 84. Характеристика вспомогательного обслуживающего процесса . 12РазвернутьСвернуть
5. Переработка нефти на ООО «ТНК-ВР».14
6. Разведка и добыча на ООО «ТНК-ВР».15
6.1 Запасы.15
6.2 Добыча и переработка.16
6.3 Газ.19
7. Продажа нефти и нефтепродуктов.21
ЗАКЛЮЧЕНИЕ .24
СПИСОК ИСПОЛЬЗУЕМЫХ ИСТОЧНИКОВ.25
-
Курсовая работа:
Разработать и спроектировать скруббер для очистки отходящих газов аммиака и мела из сушилки.
90 страниц(ы)
ВВЕДЕНИЕ
1 АНАЛИТИЧЕСКАЯ ЧАСТЬ…
1.1 Историческая справка…
1.2 Выбор и обоснование метода производства…1.3 Характеристика сырья, полуфабрикатов и готовой продукции.РазвернутьСвернуть
2 РАСЧЕТНО-ТЕХНОЛОГИЧЕСКАЯ ЧАСТЬ….
2.1 Описание технологической схемы производства азофоски….
2.2 Внесенные изменения по сравнению с аналогом их обоснование ….
2.3 Техническая характеристика сырья….
3 РАСЧЕТ ТЕХНОЛОГИЧЕСКОГО ОБОРУДОВАНИЯ….
3.1 Расчет материального баланса….
3.2 Расчет вихревого контактного устройства нижней ступени….
3.3. Расчет переливных устройств….
3.4 Расчет штуцеров….
3.5 Расчет теплового баланса….
3.6 Механический расчет…
3.7 Расчет фильтрующих элементов….
4 ТЕХНИКО-ЭКОНИЧЕСКИЕ ПОКАЗАТЕЛИ….
5 ТЕХНОЛОГИЧЕСКАЯ БЕЗОПАСНОСТЬ….
ЗАКЛЮЧЕНИЕ….
СПИСОК ИСПОЛЬЗОВАННЫХ ИСТОЧНИКОВ….
-
Задача/Задачи:
ЗАДАЧИ ПАВЛОВ РОМАНКОВ РАЗДЕЛ 3 Гидромеханические процессы
1 страниц(ы)
3.1. Найти соотношение диаметров частиц свинцового блеска (р = 7800 кг/м3) и кварца (р = 2600 кг/м3), осаждающихся с одинаковой скоростью: а) в воздухе; б) в воде, считая, что осаждение происходит при Rе < 0,2.3.2. С какой скоростью будут осаждаться шарообразные частицы кварца (р = 2600 кг/м3) диаметром 10 мкм; а) в воде при 15 °С; б) в воздухе при 15 и 500 °С?РазвернутьСвернуть
3.3. Какой должна быть скорость воздуха в вертикальной трубе пневматической сушилки, чтобы обеспечить перемещение кристаллов плотностью 2000 кг/м3 с наибольшим диаметром 3 мм? Температура воздуха 60°С. Скорость воздуха должна быть на 25% больше скорости витания частиц.
3.4. Рассчитать скорость восходящего потока воздуха в воздушном сепараторе, необходимую для отделения мелких (d < 1 мм) частиц апатита от более крупных. Температура воздуха 20 °С. Плотность апатита 3230 кг/м3.
3.5. Каким должно быть расстояние между полками пылевой камеры (см. рис. 3.9), чтобы в ней оседали частицы колчеданной пыли диаметром более 15 мкм? Остальные условия такие же, как в примере 3.6.